Made with natural clay sourced from the rich hills of Central Kenya
These custom pieces are made from ceramic clay, a naturally occurring material. Ceramic clay is durable and keeps the colors on your jewelry bright, shiny and glossy for years to come. My dream is that ceramic jewelry can compliment a woman’s natural beauty every minute, and can be a valuable heirloom to be handed down from a mother to her children.
I want to make every woman feel beautiful wearing jewelry that suits her personal style. I do this with ceramic jewelry, because it can be twisted, moulded and cast into any form imaginable. Just like a flower, every ceramic piece is unique. Every item is different from the next, and I love this uniqueness in our pieces, just like in every woman. Since ceramic also comes from natural earth, my jewelry also brings you back in touch with yourself.
It starts with creative inspiration
My process starts with the product design, sketches, and drawings for shapes. I create a lot of inspiration mood boards on Pinterest, getting inspiration from different elements like nature, animals, flowers, plants, artists, and illustrators among others. Once I have an idea in my mind, I start shaping and playing with the clay.
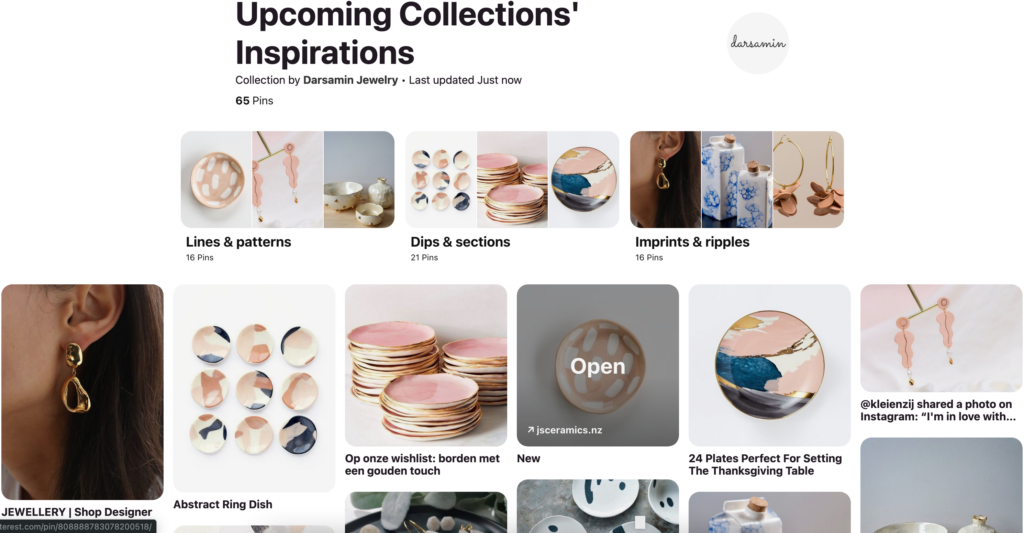
Upcoming Collections’ Inspirations on our Pinterest
Mixing and shaping
It can take up to 7 days between the moment I start with our handmade processes and when my ceramic pieces are finished with their gold-plated findings. First, I start with raw clay; I need to make it softer by hand, so it is easier to work with. I create a thin clay sheet where I’ll be modeling all our pieces.
Bisque firing
Once I have the earrings pieces cut, I make sure they have a proper shape, thickness, and finishing. I wait for the pieces to dry, then they go for the first kiln session.
They are fired in a high-temperature kiln at over 1000°C in order to harden. Each kiln burning session takes a day while the temperature goes up and down, then I can open the kiln again. This is a slow process that makes sure the pieces’ quality evens out.
Special glazing & firing
When they are completely dry, I paint waterproof or decorative glazes on the hardened pieces to give them colour & shine. After the glaze, they go once again to the kiln and the dried glaze is hardened in a second firing.
And finally, assembly
The ceramic pieces are fitted with accessories to create the final jewellery items.